ビーズミルの機械的な性能要因と製品の品質要因
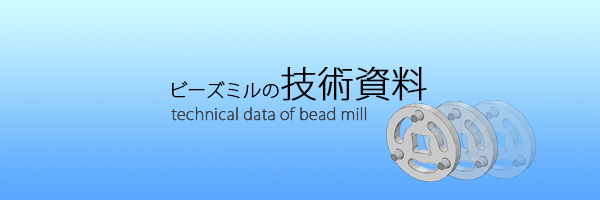
ビーズミルの分散・粉砕性能と製品の品質を左右する要因には、ビーズミルの機械的な性能要因と製品の品質要因とがあります。この2つが合致することで、目的の処理物製品を得ることができます。
ビーズミルの性能要因
ビーズミルの機械的な性能要因は、個々のミルの特長に左右されます。
ミルにはそれぞれの特長があり、それはミルの構造(撹拌槽型、流通管型、アニュラー型、撹拌機構、ビーズ分離機構、冷却方式)、運転条件(ミル内供給量と滞留時間、温度と発熱の制御)、プレミキシング、ビーズ(材質、径)、ビーズ充填量などがあります。
中でもプレミキシング、撹拌機構の形状と回転数(ディスクやローターへの周速)、粒子の硬さと周速、ミル内滞留時間などの影響が大きいといわれています。
低速運転と高速運転
AIMEXでは、ピン付きディスクの採用により、低速運転が可能です。低速運転の利点は以下の通りです。
|
弊社独自の技術「ピン付ディスク」については、こちらに詳しく記載されています。
このように低速運転のメリットは多いですが、硬い1次粒子や結合の強い凝集粒子(aggregate)は高速運転でなければなりません。高速運転では発熱が高く、粉砕室部品やビーズの摩耗が顕著になり、運転動力が大きくなりますが、砕料に強いエネルギーを与えるためには必要なことです。
砕料粒子の硬さと撹拌機構の周速
1999年頃まで、撹拌機構の周速は速いほど粉砕効果が優れていると考えられていました。重質炭酸カルシウムやカーボンの粉砕では、明らかに撹拌機構の周速が速いほど粉砕速度が速いです。
硬い砕料粒子は撹拌機構の周速が速いほど粉砕効果が高いですが、軟らかい砕料粒子は撹拌機構の周速が速いと粒子に与えるエネルギーが強すぎて再凝集が起きてしまいます。
酸化チタンは緩い凝集体です。平均1次粒子径が0.3μmの酸化チタンを0.5mmφガラスビーズと0.5mmφジルコニアビーズで解砕すると、比重の大きいジルコニアより比重の小さいガラスビーズが微粒子化します。ガラスビーズ、ジルコニアビーズともに最適周速があります。
1997年頃、1次粒子が15nmの酸化チタンが開発されましたが、粉体では数μmの凝集粒子となってしまいました。
解砕実験はジルコニアビーズを用いて、ディスク周速を7.0~12.0m/secで行いました。その結果、ビーズ径に係わりなくディスクの周速が低いほど微粒子化し、ビーズ径は0.5mmφよりも0.3mmφが微粒子化しました。この解砕実験でディスク周速に対する考え方が誤りであることが分かりました。
この結果から、軟らかい1次粒子や結合の弱い凝集粒子は強いエネルギーを与えるよりもソフトなエネルギーで処理することが望ましいことが明らかです。強いエネルギーを与えると破砕によって生じた新生面の活性化エネルギーで再凝集することから、粒子径は小さくなりません。硬い1次粒子や結合の強い凝集粒子は、強いエネルギーを与えることによって微粒子化されます。したがって軟らかい粒子には低周速、硬い粒子には高周速が望ましいと言えるでしょう。
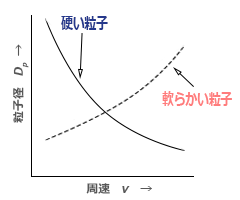
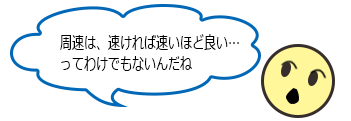
ミル内滞留時間
ビーズミル内滞留時間は粉砕性能に大きな影響があります。かつては撹拌ミルは連続粉砕でサブミクロンを得る可能性のある数少ないミルであるから、滞留時間を長くするためには流通管型としてできるだけミルを長くすることが望ましいと言われたこともあります。この考えはミル内を一度通過すさせることで目標の粒子径を得る時に効果を発揮します。
ミルを長くする代わりに、ミル内を複数回通過させるパス方式で滞留時間を長くすることも行われています。
製品の品質要因
製品の品質要因はフォーミュラー、粉体と溶媒、固形分濃度、粘度、分散剤、プレミキシングの良否、温度と発熱の制御、ミル内供給量と滞留時間、プレミキシング、ミルの構造と運転条件、材質、ビーズ(材質、径、充填量)、摩耗とコンタミネーションなどで、ビーズミルの特徴と、粉体、溶媒、添加剤などが大きな影響を及ぼします。フォーミュラー、粉体と溶媒、固形分濃度と粘度などはビーズミルユーザーの決定事項であり、ビーズミルメーカーにはブラックボックスです。
<引用・参考文献>
中山勉:「超微粒子・ナノ粒子をつくる ビーズミル」,工業調査会
■ 次の記事「ビーズミルによるメカノケミカル」≫
■ 前の記事「ビーズミルの歴史」≫
■ ビーズミル技術資料一覧ページへ ≫