nanotech2016【3】迅速な実験のために
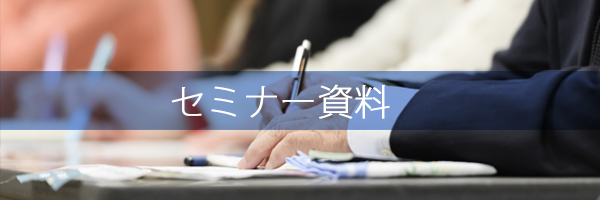
迅速な実験のために
ユーザーが設定可能かつ結果に影響を与える因子
ビーズ材質
高比重のものが分散効果が高い。コンタミネーションの最も多い箇所。
製品特性、摩耗、コストを考えて選定する必要がある。
ジルコニアかガラスが一般的。
ビーズ量
ビーズ量に比例して処理効率が上昇する傾向にあるが、同時に異常発熱や摩耗の原因となる。
ビーズ径
処理前粒子径の10倍、目標粒子径の1000倍の大きさが目安。
硬い試料の場合は大きいビーズで大きなエネルギーを与えなければ良い結果が得られない場合がある。
大きいエネルギーを必要としない分散処理、あるいはナノレベルまでの分散などで
大きいエネルギーを与えたくない場合においては微小ビーズが有効である。
ディスク周速
対象物によって適正周速は異なる。高周速は凝集原因の1つでもあり、
発熱、摩耗のことを考えればできる限 り低周速での処理が望ましい。
スラリー配合
凝集や増粘などミル処理によって生じる現象は、機械的条件で回避可能な場合もあるが、
ウエイトの大部分は配合にかかっている。特に、ナノレベルの分散は添加剤による影響が大きい。
生産効率と分散効率にも大きく影響する。
固形分濃度変化によっても分散効率は変化し、生産効率を踏まえた決定が必要。
スラリー粘度
スラリー配合により増粘する場合もあるが、処理前からの極度の高粘度はミルの安定運転上好ましくない。
圧力上昇や効率低下の原因にもなる。
ポンプ吐出流量
循環運転方式の場合、吐出流量を多く設定し、循環回数を増やした方が
粒度分布がシャープになる傾向がある。圧力変化を伴うファクターであり、
増やし過ぎるとビーズの偏りを引き起こしたりする。メカシール圧とのバランスも重要。
複雑に絡むビーズミルの性能因子~どのように条件を決定するか?~
STEP1
粉砕 or 解砕の見極め
着眼点
投入エネルギーに対して粒径進捗の反応が良いか?
粉砕:処理強度重視 ⇔ 解砕:処理頻度重視
(例:周速を上げるほど微粒子化が進捗する≒粉砕)
経験則として粉砕処理のほとんどの場合でΦ0.1mm以下のビーズは効果薄
STEP2
ビーズ径の選定
着眼点1
目安は目標粒子径の1000倍(目標0.5μm⇒ビーズΦ0.5mm)着眼点2
処理前粒子径(最大径も考慮)と目標粒子径の比着眼点3
粘度高粘度処理で小径ビーズの使用は効果薄 着眼点4
エネルギー過多で結晶構造は変化しないか?
・一般的に、数百μm~ミリオーダーの粒子粉砕にはΦ1.0mm以上が必要
・ビーズの動きが極端に悪くなるようでは×
STEP3
濃度の決定
着眼点1
処理経過によって極端に増粘するか?
増粘が極端な場合:同一ビーズで処理可能か?圧力・温度は大丈夫か?

濃度によって到達限界粒子径が変わるか?
一般的に、濃厚系の方が分散速度が遅いが、生産効率は高い。
濃度が到達限界粒子径へ影響することも多々ある。
STEP4
周速(回転数の設定)
着眼点1
結晶構造は変化しないか?着眼点2
再凝集しないか?着眼点3
温度制限はクリアできるか?
・ナノ分散において、結晶性の維持・再凝集防止のために低周速運転が主流
・ビーズの動きが極端に悪くなるようでは×
・粉砕の場合は高周速が基本。発熱・コンタミの問題から、どれだけ低周速で高効率処理できる装置かが問われる。
STEP5
送液量の決定、運転方式の決定(パスor循環)
着眼点
目標までの到達時間(パス回数)は?
目標までの到達時間が長い(10パス以上)場合:大流量循環運転が主流
方式 | 管理方法 | メリット | デメリット・注意点 |
---|---|---|---|
大流量循環運転 | 時間 | ・処理効率アップ ・シャープな粒度分布(注意) ・タンク1つで手間いらず |
・圧力上昇 ・温度上昇 ・ビーズの偏り ・摩耗増 ・目標までの循環回数 ・粗大粒子残の可能性 ・N倍処理≠時間N倍 |
パス運転 | パス回数 | ・1パス処理でシンプルな生産ライン ・N倍処理≠時間N倍 ・未処理粒子がない |
・多パス運転時はタンク切替が必要(自動化可能) ・初期コスト(撹拌機、タンク等)増 |
STEP6
結果分析(一例のご紹介)
途中から増粘が顕著だった
・過分散で再凝集したか?
・増粘によってビーズの動きが悪くなった?
・濃度を下げないと処理できないか?
・大径ビーズを使用すれば期待できるか?
途中で進捗が頭打ちになった(粒径進捗が極端に遅い)
・もっと小径のビーズの方が効果的?
・進捗が遅いのはエネルギー不足?
・希薄系にしたら分散できるかも?
粗大粒子が残っている。もっとシャープな分布にしたい
・循環回数が不足していたか?
・送液量はこれ以上増やせないか?
・パス運転で確認するか?
・選定したビーズ径では粗大粒子の対してはエネルギー不足?
AIMEXはバッチ式による条件検討テストを推奨します
- 圧倒的に部品点数が少なく、分解洗浄が楽(洗浄10分、分解組立30秒)
- 水道水での冷却も可。100V電源と簡単操作で設置後すぐに運転開始。
- 多筒同時運転可(最大6条件同時処理)
ポンプがあると…
- 高密度試料などで沈降滞留物が悪影響する!?(配管詰まりなど)
- 「送液量L/min」によっては余計なトラブルも発生!?(発熱・圧力上昇)
- 条件数が減って検討しやすくなる
- 対応ビーズ径を気にしなくて良いため、柔軟な検討が可能
- ビーズは後からフィルタリングで除去
- 30mLから処理可能で、高価な試料にも最適
- 装置内残留スラリーによるロスも最低限に
- 傾向をつかむ⇒後々の生産条件検討の迅速化
事例
A社の場合|ビーズミル初検討- 処理物: 無機酸化物スラリー 10 wt%
- 処理前粒径: D50 = 6 mm, D99 = 50 mm
- 目標粒子径: D50 = サブミクロン(小径であればあるほどいい)
- 将来的には量産 ⇒ 連続機
バッチ式TSGによる多筒同時運転で処理可否検討 さらに短時間にビーズ径比較=連続機選定 |
<基本データ>
処理物 | 無機酸化物スラリー10wt% |
---|---|
使用機種 | バッチ式TSG-6U |
ディスク周速 | 4.2m/s |
ビーズ | φ1.0,0.5,0.3,0.1mmジルコニアビーズ |
目標粒子径 | D50<1μm |
試験結果
処理最適ビーズはΦ0.5 or 0.3 mm
•Φ 0.1 mmはエネルギー不足、Φ 1.0 mmはビーズ充填数が低いため処理速度で負けた
•粘度上昇等なし。固形分濃度増加で収率アップの可能性
ビーズ自体のコストパフォーマンス・ハンドリングは Φ 0.5 mm > Φ 0.3 mm
⇒Φ0.5 mm採用 ・ 選定連続機:NVM
循環量と処理量
D50はほぼ同一
D90は処理量が多いほど大→ 循環運転では処理量が増えると処理むらが大きくなる
D90の差は経時的に解消